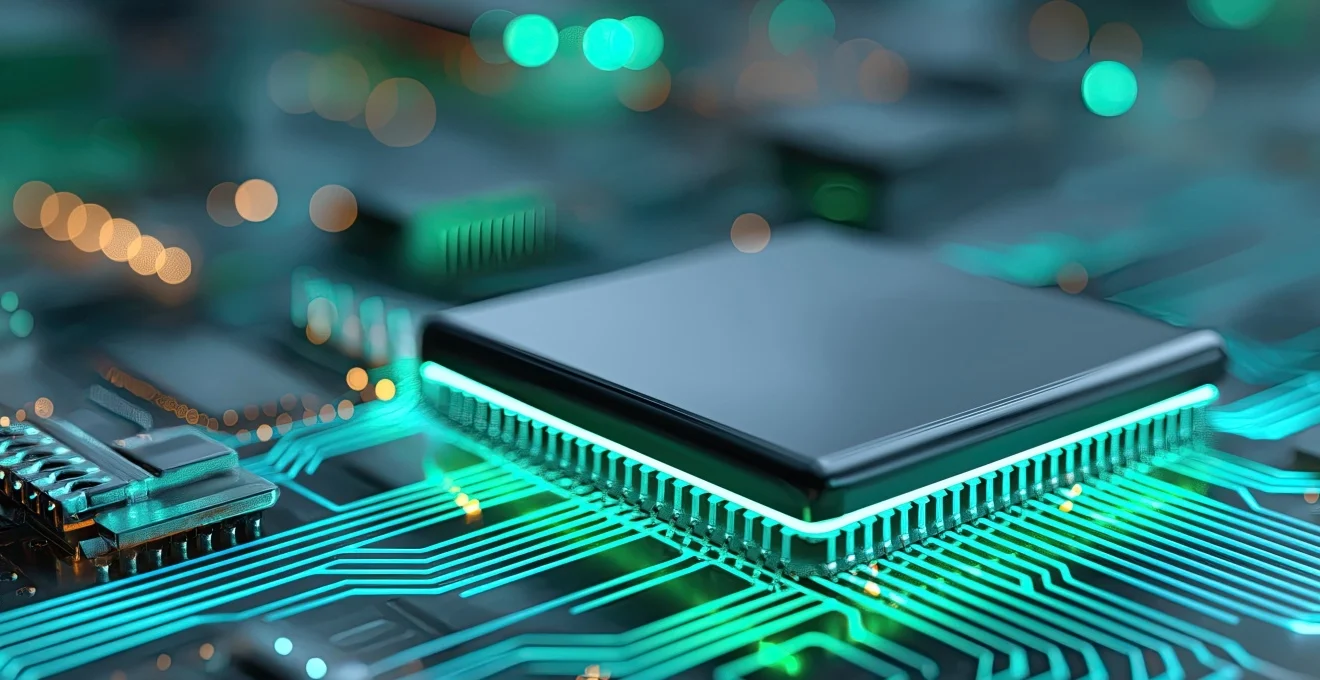
The imposition of tariffs on printed circuit boards (PCBs) has sent ripples through the global electronics industry, affecting manufacturers and consumers alike. As a cornerstone of modern electronics, PCBs play a crucial role in everything from smartphones to industrial machinery. The introduction of these tariffs has sparked a complex chain reaction, altering production costs, consumer prices, and global supply chains. Understanding the far-reaching implications of PCB tariffs is essential for businesses and consumers navigating this new economic landscape.
PCB tariffs impact on manufacturing costs
The implementation of PCB tariffs has significantly increased manufacturing costs across various industries. These additional expenses stem from the higher prices of imported PCBs, which are essential components in countless electronic devices. Manufacturers now face the challenge of absorbing these increased costs or passing them on to consumers, a decision that can impact their competitiveness and market share.
For many companies, the tariffs have led to a reevaluation of their supply chain strategies. Some are exploring alternatives to Chinese PCB suppliers, looking to countries like Vietnam, Taiwan, or Mexico. However, shifting production is not a simple task and often comes with its own set of challenges, including quality control issues and logistical hurdles.
The impact of these tariffs varies depending on the type of PCB and its complexity. For instance, multilayer PCBs, which are more technologically advanced and often used in high-end electronics, may see a more significant price increase compared to simpler, single-layer boards. This disparity can lead to varying degrees of cost pressure across different sectors of the electronics industry.
Moreover, the tariffs have spurred innovation in PCB design and manufacturing processes. Companies are now investing in research and development to create more efficient PCB designs that require less material or can be produced domestically to avoid tariffs altogether. This push for innovation, while potentially beneficial in the long term, adds to the short-term costs for manufacturers.
Repercussions of PCB duties on consumer prices
The ripple effect of PCB tariffs extends beyond manufacturing costs, directly impacting consumer prices across a wide range of electronic products. As manufacturers grapple with increased production expenses, many are forced to raise prices to maintain profitability. This price hike is particularly noticeable in consumer electronics, household appliances, and automotive sectors, where PCBs are integral components.
According to industry analysts, the average price increase for consumer electronics due to PCB tariffs ranges from 3% to 8%, depending on the product category and the proportion of PCB costs in the overall manufacturing process. This increase may seem modest, but it can significantly affect consumer purchasing decisions, especially for big-ticket items.
Electronics industry hit by PCB levies
The electronics industry has been particularly hard hit by PCB tariffs. Smartphones, laptops, tablets, and other consumer electronics rely heavily on PCBs, making them susceptible to price fluctuations. Major manufacturers have reported increased production costs, with some opting to absorb a portion of these expenses to remain competitive, while others have reluctantly raised prices.
For instance, the smartphone market has seen an average price increase of 5-7% due to PCB tariffs. This rise has led to extended upgrade cycles as consumers hesitate to purchase new devices at higher price points. Similarly, the computer industry has experienced price hikes, with some laptop models seeing increases of up to $50-$100 per unit.
The impact extends to smaller electronics as well. Items like smart home devices, wearables, and gaming consoles have all seen price adjustments to compensate for the increased cost of PCBs. This trend has prompted some consumers to delay purchases or seek alternatives, potentially slowing the adoption of new technologies.
Household appliances prices surge after tariffs
The household appliance sector has not been immune to the effects of PCB tariffs. Modern appliances, from refrigerators to washing machines, increasingly rely on sophisticated electronic controls that incorporate PCBs. As a result, manufacturers have been forced to reevaluate their pricing strategies in light of the increased component costs.
Industry reports indicate that the average price of major household appliances has risen by 3-5% since the implementation of PCB tariffs. This increase is particularly noticeable in smart appliances, which contain more advanced PCBs. For example, a smart refrigerator that previously retailed for $2,000 might now cost $2,060 to $2,100, a significant jump for budget-conscious consumers.
The price surge has led to changes in consumer behavior, with some opting for lower-end models or delaying replacements of older appliances. This shift has implications not only for consumer wallets but also for energy efficiency and technological adoption in homes.
Automotive sector faces higher input costs
The automotive industry, already grappling with various economic pressures, has been further challenged by PCB tariffs. Modern vehicles rely heavily on electronic systems for everything from engine management to infotainment, making PCBs an essential component in car manufacturing.
The impact of PCB tariffs on car prices varies depending on the vehicle type and level of electronic sophistication. On average, consumers can expect to see a price increase of $100 to $300 per vehicle, with luxury and electric vehicles experiencing the higher end of this range due to their more extensive use of electronic components.
This price increase comes at a time when the automotive industry is pushing for greater electrification and autonomous driving capabilities, both of which require advanced PCBs. The added cost pressure could potentially slow down innovation in the sector or lead to compromises in other areas of vehicle production to maintain competitive pricing.
Global supply chains disrupted by PCB tariffs
The implementation of PCB tariffs has had a profound impact on global supply chains, forcing companies to reevaluate and often restructure their sourcing strategies. This disruption has led to a complex realignment of manufacturing and distribution networks across the electronics industry.
One of the most significant changes has been the shift away from Chinese PCB manufacturers, who have long dominated the global market. Companies are now exploring alternative sources in countries like Vietnam, Taiwan, and India. This geographical diversification aims to mitigate the impact of tariffs but comes with its own set of challenges, including quality control, capacity limitations, and logistics.
Icape-group.com provides valuable insights into how companies are navigating these new tariff realities. Many firms are adopting a “China plus one” strategy, maintaining some production in China while establishing secondary manufacturing hubs in other countries to spread risk and reduce tariff exposure.
This shift has led to increased complexity in supply chain management. Companies now must juggle multiple suppliers across different countries, each with its own regulatory environment and logistical considerations. The need for more sophisticated supply chain management tools and strategies has grown, adding another layer of cost and complexity to the manufacturing process.
Moreover, the disruption has exposed vulnerabilities in just-in-time manufacturing models. With longer lead times and increased uncertainty in the supply chain, some companies are reverting to holding larger inventories of critical components, including PCBs. This shift away from lean manufacturing principles represents a significant change in operational strategy for many firms.
Domestic PCB production capacity limitations
As companies seek alternatives to imported PCBs to avoid tariffs, attention has turned to domestic production capabilities. However, this shift has exposed significant limitations in the domestic PCB manufacturing sector, particularly in countries that have long relied on imports.
In the United States, for example, domestic PCB production capacity has declined over the past two decades as manufacturing shifted overseas. Rebuilding this capacity is a complex and capital-intensive process that cannot be accomplished quickly. The current domestic PCB industry lacks the scale and, in some cases, the technological capabilities to meet the sudden surge in demand.
The challenges of expanding domestic PCB production include:
- High initial investment costs for advanced manufacturing equipment
- Shortage of skilled labor in PCB manufacturing
- Limited domestic supply of raw materials needed for PCB production
- Regulatory hurdles and environmental considerations
These limitations have led to a situation where domestic PCB prices are often significantly higher than those of imported boards, even after accounting for tariffs. This price differential puts pressure on manufacturers who are trying to balance cost considerations with the desire to secure a more stable, domestic supply chain.
Some governments and industry groups are pushing for initiatives to boost domestic PCB manufacturing capabilities. These efforts include investment incentives, workforce development programs, and research grants aimed at advancing PCB technology. However, the results of these initiatives will take time to materialize, leaving many manufacturers in a challenging position in the short to medium term.
The situation has also sparked debates about the strategic importance of maintaining domestic capabilities in critical technologies like PCB manufacturing. Some argue that over-reliance on foreign suppliers for essential components poses national security risks, particularly for defense and aerospace applications.
Lobbying efforts surrounding PCB tariff policies
The introduction of PCB tariffs has sparked intense lobbying efforts from various industry stakeholders, each seeking to influence policy decisions in their favor. These efforts reflect the complex interplay of economic interests, national security concerns, and global trade dynamics.
On one side of the debate are domestic PCB manufacturers and their allies, who argue that tariffs are necessary to level the playing field and revitalize the U.S. PCB industry. They contend that years of unfair competition from subsidized foreign producers have eroded domestic manufacturing capabilities, and that tariffs provide a much-needed opportunity for recovery and growth.
Opposing these views are electronics manufacturers, consumer electronics companies, and trade associations representing industries that rely heavily on imported PCBs. These groups argue that tariffs increase costs, stifle innovation, and ultimately harm U.S. competitiveness in the global market. They advocate for more targeted approaches to supporting domestic PCB production without resorting to broad tariffs.
The lobbying landscape is further complicated by geopolitical considerations, particularly concerns about technology transfer and national security. Some policymakers and defense industry representatives argue for maintaining and expanding domestic PCB production capabilities as a matter of strategic importance.
Key points in the lobbying debate include:
- The impact of tariffs on U.S. jobs and economic growth
- The potential for tariffs to spur domestic investment in PCB manufacturing
- The effects of higher PCB costs on downstream industries and consumers
- The role of PCBs in critical technologies and national security applications
- The need for a comprehensive strategy to support U.S. high-tech manufacturing
As lobbying efforts continue, policymakers face the challenge of balancing these competing interests while navigating the complexities of global trade relationships. The outcome of these debates will have far-reaching implications for the future of the PCB industry and the broader electronics manufacturing sector.
The ongoing discussions underscore the need for nuanced policy approaches that consider both the immediate economic impacts of tariffs and the long-term strategic goals of maintaining a robust domestic manufacturing base. As the situation evolves, stakeholders across the industry continue to closely monitor policy developments and adjust their strategies accordingly.